The integration of robots in human-centered environments is becoming increasingly prevalent. With this transition, mobile manipulation and compliant control has become essential. This is particularly crucial for ensuring robust performance coupled with safety in unstructured, dynamic environments where the robot operates in close proximity to humans.
Compliance refers to the ability of a robot to interact with its environment in a flexible and adaptable manner. It is usually achieved through indirect force control methods such as admittance and impedance control. Admittance control enables the robot to adapt its behaviour based on sensed forces, allowing it to yield or move in response to external forces. Impedance control regulates the robot’s interaction with its environment by managing the relationship between applied forces and resulting movements, in other words the robot’s “stiffness” to external forces.
These methods typically require contact information that is derived from measurements of the joint torques or from a force/torque sensor mounted at the end-effector. Such equipment can often be expensive and might not be available in off-the-shelf robots. What further presents a challenge is what type of control mode is supported by the robot.
To address these challenges, the Autonomous Multi-Robots Lab at the Delft University of Technology is working on a cost-effective approach to address compliance for mobile manipulators and velocity-controlled mobile bases without having to add force/torque sensors.
Dingo-O: The Ideal Platform for Human-Centered Environments
The team used Dingo-O for their base as part of the mobile manipulator. Dingo-O is a sleek, lightweight, omni-directional indoor platform ideal for human-centered environments. The team highlighted how easy it was to set up and use the platform. The robot was equipped with a Kinova Gen 3 lite arm.
Using the mobile manipulator, the team developed a calibration method that would enable the application of impedance control on current-controlled manipulators. This method estimates the direct correlation between the actuator current and the resulting joint torque as well as the friction encountered by the arm as it moves its joints. It utilizes the robot’s model and earth’s gravity to estimate the ratio between the actuator current and the resulting torque. Furthermore, the calibration method also incorporates techniques to adjust for Center of Mass (COM) displacements, ensuring that the robot’s behaviour is accurately modelled and controlled.
The team developed two operational modes for interacting with the robot:
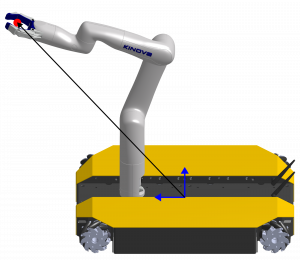
Figure 1: Guidance Mode
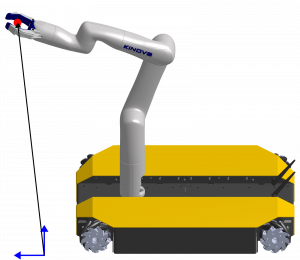
Figure 2: Tracking Mode
A guidance mode to guide the system around the workspace through interacting with the arm,
And, a tracking mode to execute a tracking task, allowing the arm to follow a specific path.
Both modes are compliant in the case of contact.
Check out these videos of the team showcasing the two operational modes:
A Triumph In Compliance-Drive Mobile Manipulation
The team was able to develop a holistic, cost effective approach to addressing compliance for mobile manipulators using off-the-shelf parts. They were able to introduce a calibration method that enables the application of impedance control on current-controlled manipulators, and therefore no force/torque sensors are required.
Demonstrating the reliability of their method, the team was able to present two operational modes for interacting with the mobile manipulator. This allowed a human to guide the robot through interaction with the manipulator and expand the manipulator’s operational range. The compliance of the impedance controller was validated, showcasing its ability to track a target with precision, achieving accuracy within a 5 mm range when uninterrupted by external forces
Their work not only promotes cost-effectiveness, accessibility and adaptability using off-the-shelf parts, but also significantly enhances the usability and efficacy of mobile manipulation in real-world scenarios such as collaborative robotics and assistive applications.
The Future
The team’s work was accepted by the 2024 IEEE/RSJ International Conference on Intelligent Robots and Systems (IROS 2024). In the future, the team would also like to investigate how their calibration method could be applied to the mobile bases.
If you would like to learn more about the Autonomous Multi-Robots Lab at Delft University, you can visit their website here.
If you would like to learn more about Project Harmony, you can visit their website here.
If you would like to learn more about Dingo, you can visit our website here.
The team members involved in this research project include Jelmer de Wolde (Master student, graduated), Luzia Knoedler (PhD student), Saray Bakker (PhD student), Andreu Matoses Gimenez (PhD student), Javier Alonso-Mora (associate professor).