In the bustling world of rail transportation, efficiency is paramount. Rail yards – those crucial hubs where trains are assembled, sorted, and dispatched – play a pivotal role in ensuring that freight and passengers reach their destinations on time. However, the complex operations within these yards are often manual and can be a bottleneck, leading to delays and increased operational costs. Enter Husky Observer – our fully integrated robotics platform that enables developers to accelerate the deployment of automated inspection solutions for industrial applications.
Husky Observer Optimizes Processes at Rail Yard
Husky Observer is a rugged, autonomous inspection system that can navigate autonomously to GPS coordinates and collect data using onboard cameras and sensors while avoiding obstacles. Husky Observer uses our OutdoorNav autonomy software – a flexible and powerful GNSS based autonomy stack for outdoor environments.

Husky Observer pointing camera towards train car links.
Our team recently had the opportunity to deploy Husky Observer at a Class 1 automotive rail yard in the southern United States. The customer was looking at applications for an autonomous inspection platform including measuring positions of assets, safety checks, and RFID scanning. Specifically, they were looking for an automated solution for measuring the distance between freight cars. If the freight cars are parked too close or too far from each other, they have to wait until the following night for the train operators to return to adjust the spacing to allow for the bridge plate to be installed. Bridge plates are a flat aluminum structure allowing the safe and efficient driving of vehicles between freight cars.
Waiting for the train conductors to return often delays the transport trucks’ ability to pick-up shipments. By automating this process, beyond having someone in a golf cart checking the spacing during the day, the rail yard can better optimize their workflow. The robust design, safety features, and autonomy capabilities of Husky Observer make it a great choice for this outdoor industrial facility and use case.
Setting Up the Autonomous Mission
The first task was to create the mission for Husky Observer by defining the allowable driving areas in the rail yard environment via Clearpath’s OutdoorNAV autonomy software. Inspection locations and tasks were then defined on the interactive map by the operator. At each inspection location, Husky Observer was programmed to position its integrated pan-tilt-zoom camera and capture images between the railcars.

AMR allowable driving areas on OutdoorNAV autonomy software user interface.
Running the Mission
The robot was then ready to be sent out on its mission. Using its onboard sensor suite, the robot navigated autonomously through the GNSS constrained environment and stopped at inspection points to collect data. The operator conveniently monitored the robot’s progress remotely via the web user interface.
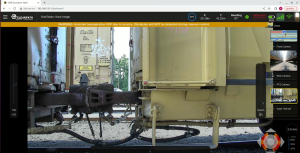
View of train car links from Husky Observer camera on OutdoorNAV autonomy software user interface.
Rail terminals are difficult environments for robot deployment as localization can be a challenge without strong GNSS (GPS) signals due to the 20 feet tall metal train cars. A static map is not dependable for localization as the primary features, trains and cars, are not stationary. The onboard localization module fuses GNSS data, visual odometry, IMU data, and wheel encoder data to provide consistent localization estimates even in these challenging environments. This results in a system with other sources of localization to rely on during partial GNSS outages.
LiDAR data was used to measure train spacing at inspection locations and also to detect any obstacles along the way. Additional sensor data can be gathered for further analysis, including positional measurements, with ROS (robot operating system).
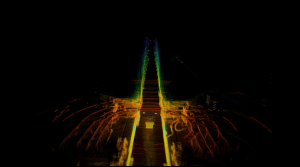
3D point cloud visualization from onboard 360° lidar of Husky Observer navigating between train cars.
Analyzing the Data
Husky Observer comes with a built-in computer that can be upgraded with a GPU (graphics processing unit). In this use case, a powerful, GPU-enabled secondary computer was implemented on the robot for 3D point cloud processing and machine learning processing of images. With this, the team is able to implement trained AI models specific to the application. The system can also be set up to send data live to a cloud service or downloaded after missions for post processing on another computer.
Check out the robot in action at the rail yard in the video below:
To learn more about how Husky Observer can transform operations in rail yard environments or other industrial facilities, contact our team.